When it comes to steel treatment, surface preparation is the essential first step. Steel can be treated in a number of ways, depending on its intended application, but all steel sections need to be prepped to ensure that dirt, dust, rust, and grease don’t interfere with the surface when it is coated.
The steel surface preparation methods range from simple chemical cleaning to more abrasive methods such as abrasive grit blasting. Let’s take a look at the different types and what’s involved.
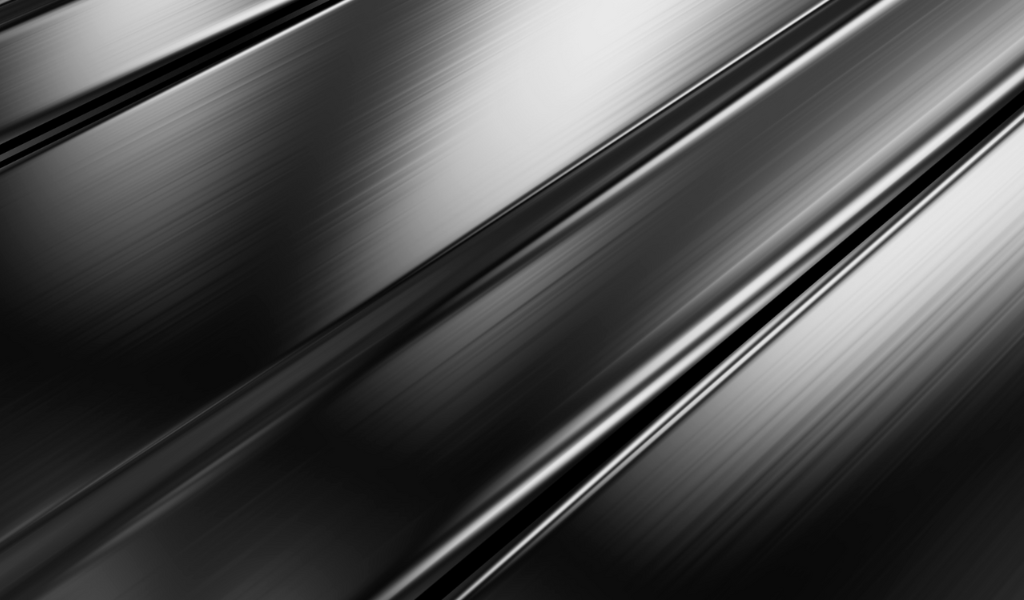
Surface preparation is the essential first step for steel treatment. Let’s take a look at the different types and what’s involved.
What Kind of Contaminants Need to Be Removed?
Rust – All steel is susceptible to corrosion if it is not treated beforehand. There are many different types, ranging from uniform attack corrosion, to pitting corrosion. The type of corrosion will dictate what rust grade the steel is. Some grades should be avoided, such as pitted steel, which can be very difficult to clean.
Mill Sale – Mill scale is the flaky surface of hot rolled steel, consisting of different iron oxides. It is a nuisance when the steel needs to be processed. Any paint applied over it is wasted, since it will come off with the scale as moisture-laden air gets under it. Hence it needs to be removed.
Grease, Oil, Dirt and Dust – When preparing steel, anything that might prevent the paint wetting out or adhering to the surface needs to be removed. This includes grease and oils, as well as dirt, dust and salts.
What Are The Common Methods of Steel Preparation?
Solvent Cleaning – Before any further cleaning or preparation, steel sections are first wiped down with acetone, a thinner, or another type of solvent. This helps remove mill scale, oxides, and some corrosion.
Abrasive Grit Blasting – Grit blasting is the most effective method for removal of particularly difficult dirt, mill scale, rust and old coatings and other impurities. This is achieved using a shot-blasting machine, which the raw steel is passed through.
Prior to blasting, steelwork needs to be cleaned of any oils or grease. It is then blasted with shot or another abrasive material, which bombardes the steel surface, removing any impurities. The machine then brushes off any debris. There are all different types of classifications for blast cleaning a steel section, which will depend on what it is being used for, and what is being done afterwards (such as painting, coating or welding).
Hand & Power Tool Cleaning – Scrapers, wire brushes and other hand held tools are relatively ineffective in removing mill scale or corrosion. However, power tools like rotary brushes, rotary grinders, and needle guns may be useful for cleaning hard-to-reach places where grit blasting is not possible.
Acid Pickling – This involves immersing the steel in a bath of suitable inhibited acids that dissolve or remove the mill scale and rust. This technique is normally only used for structural steel intended for hot-dip galvanising.
Flame Cleaning – This involves passing an oxy/gas flame over the steel surface. The heat causes rust scales to flake off, which can then be removed by scraping and wire brushing followed by dust removal. It is not he most efficient process and is rarely used.
Wet Abrasive Blast Cleaning – As the name implies, this is similar to the girt blasting technique, however, water is employed rather than shot. This contributes to the reduction of a dust hazard, particularly when removing lead-based paints and water-soluble contaminants. Ultra-high pressure water jetting is also used, which is favoured by some because it removes high percentages of soluble salts from the surface.
Industry Standards for Steel Preparation
Preparing steel properly is an important process and must be done correctly. Luckily, SSPC and NACE put together a handy guide to help you correctly prepare your steel for treatment.
Standard Number | Preparation Required | Description |
---|---|---|
SSPC-SP 1 | Solvent Cleaning | Removal of all visible oil, grease, dirt, soil, salts, and contaminants by cleaning with solvent, vapor, alkali, emulsion, or steam. |
SSPC-SP 2 | Hand Tool Cleaning | Removal of loose rust, loose mill scale, and loose paint, by hand chipping, scraping, sanding, and wire brushing. |
SSPC-SP 3 | Power Tool Cleaning | Removal of all loose rust, loose mill scale, and loose paint, by power tool chipping, descaling, sanding, wire brushing, and grinding. |
SSPC-SP 5/NACE No. 1 | White Metal Blast Cleaning | Removal of all visible rust, mill scale, paint, and foreign matter by blast cleaning by wheel or nozzle (dry or wet) using sand, grit or shot. For very corrosive atmospheres where high cost of cleaning is warranted. |
SSPC-SP 5 (WAB)/ NACE WAB1 | White Metal Wet Abrasive Blast Cleaning | Same level of cleanliness as SSPC-SP 5/NACE No. 1, but achieved by wet abrasive blast cleaning. Level of flash rust permissible immediately prior to coating application must be specified. |
SSPC-SP 6/ NACE No. 3 | Commercial Blast Cleaning | Removal of all visible rust, mill scale, paint, and foreign matter by blast cleaning. Staining is permitted on no more than 33% of each 9 in2 (0.005 m2 ) area of the cleaned surface. For conditions where a thoroughly cleaned surface is required. |
SSPC-SP 6 (WAB)/ NACE WAB3 | Commercial Wet Abrasive Blast Cleaning | Same level of cleanliness as SSPC-SP 6/NACE No. 3, but achieved by wet abrasive blast cleaning. Level of flash rust permissible immediately prior to coating application must be specified. |
SSPC-SP 7/ NACE No. 4 | Brush-Off Blast Cleaning | Removal of all loose contaminants while uniformly roughening the surface. Tightly adhering residues of mill scale, rust, and coatings may remain. |
SSPC-SP 7 (WAB)/ NACE-WAB 4 | Brush-Off Wet Abrasive Blast Cleaning | Same level of cleanliness as SSPC-SP 7/NACE No.4, but achieved by wet abrasive blast cleaning. Level of flash rust permissible immediately prior to coating application must be specified. |
SSPC-SP 8 | Pickling | Complete removal of rust and mill scale by acid pickling, duplex pickling, or electrolytic pickling |
SSPC-SP 10/ NACE No. 2 | Near-White Blast Cleaning | Removal of all visible rust, mill scale, paint, and foreign matter by blast cleaning. Staining is permitted on no more than 5% of each 9 in2 (0.005 m2 ) area of the cleaned surface. For high humidity, chemical atmosphere, marine, or other corrosive environments. |
SSPC-SP 10 (WAB)/ NACE WAB2 | Near-White Metal Wet Abrasive Blast Cleaning | Same level of cleanliness as SSPC-SP 10/NACE No. 2, but achieved by wet abrasive blast cleaning. Level of flash rust permissible immediately prior to coating application must be specified. |
SSPC-SP 11 | Power Tool Cleaning to Bare Metal | Complete removal of all visible oil, grease, coatings, rust, corrosion products mill scale, and other foreign matter by power tools, with resultant minimum surface profile of 1 mil (25.4 µm). Trace amounts of coating and corrosion products may remain in the bottom of pits if the substrate was pitted prior to cleaning. |
SSPC-SP 14/ NACE No. 8 | Industrial Blast Cleaning | Between SP 7 (brush-off) and SP 6 (commercial). The intent is to remove as much coating as possible. Tightly adhering contaminants can remain on no more than 10% of each 9 in2 (0.005 m2 ) area of the cleaned surface. |
SSPC-SP 14 (WAB)/ NACE WAB8 | Industrial Wet Abrasive Blast Cleaning | Same level of cleanliness as SSPC-SP 14/NACE No. 8, but achieved by wet abrasive blast cleaning. Level of flash rust permissible immediately prior to coating application must be specified. |
SSPC-SP 15 | Commercial Grade Power Tool Cleaning | Between SP 3 and SP 11. Complete removal of all visible oil, grease, dirt, rust, coating, mill scale, corrosion products and other foreign matter by power tools, with resultant minimum surface profile of 1 mil. Random staining is limited to no more than 33 percent of each 9 in2 (0.005 m2 ) of surface. Trace amounts of coating and corrosion products may remain in the bottom of pits if the substrate was pitted prior to cleaning |
SSPC-SP 16 | Brush-Off Blast Cleaning of Coated and Uncoated Galvanized Steel, Stainless Steels, and Non-Ferrous Metals | Requirements for removing loose contaminants and coating from coated and uncoated galvanized steel, stainless steels, and non-ferrous metals. Cleaned surface is free of all visible oil, grease, dirt, dust, metal oxides (corrosion products), and other foreign matter Requires a minimum 0.75 -mil (19-µm) profile on bare metal substrate. |
SSPC-SP WJ-1/ NACE WJ-1 | Waterjet Cleaning of Metals–Clean to Bare Substrate | When viewed without magnification, the metal surface shall have a matte (dull, mottled) finish and shall be free of all visible oil, grease, dirt, rust and other corrosion products, previous coatings, mill scale, and foreign matter |
SSPC-SP WJ-2/ NACE WJ-2 | Waterjet Cleaning of Metals–Very Thorough Cleaning | When viewed without magnification, the metal surface shall have a matte (dull, mottled) finish and shall be free of all visible oil, grease, dirt, rust, and other corrosion products except for randomly dispersed stains of rust and other corrosion products, tightly adherent thin coatings, and other tightly adherent foreign matter. The staining or tightly adherent matter shall be limited to no more than 5 percent of each 9 in2 (0.005 m2 ) area of the cleaned surface. |
SSPC-SP WJ-3/ NACE WJ-3 | Waterjet Cleaning of Metals–Through Cleaning | When viewed without magnification, the metal surface shall have a matte (dull, mottled) finish and shall be free of all visible oil, grease, dirt, rust, and other corrosion products except for randomly dispersed stains of rust and other corrosion products, tightly adherent thin coatings, and other tightly adherent foreign matter. The staining or tightly adherent matter shall be limited to no more than 5 percent of each 9 in2 (0.005 m2 ) area of the cleaned surface. |
SSPC-SP WJ-4/ NACE WJ-4 | Waterjet Cleaning of Metals–Light Cleaning | When viewed without magnification, the metal surface shall be free of all visible oil, grease, dirt, dust, loose mill scale, loose rust and other corrosion products, and loose coating. Any residual material shall be tightly adhered to the metal substrate and may consist of randomly dispersed stains of rust and other corrosion products or previously applied coating, tightly adherent thin coatings, and other tightly adherent foreign matter. |
SSPC-PA 17 | Conformance to Profile/Surface Roughness/Peak Count Requirements | A procedure suitable for shop or field use for determining compliance with specified profile ranges on a steel substrate. |
Source your steel from Steel Fabrication Services
Our team of expert structural steel fabricators have the experience and knowledge to answer any of your questions and will ensure that you find the best solution to suit your needs. To contact us today, simply call, fax, email or drop by our Brookvale location.
While you’re here, read more about steel and its benefits:
What’s the Difference Between Ferrous and Non-Ferrous Metals?
How To Choose the Best Type of Steel for Your Next Project
Your Guide To Steel Surface Treatments: Chemical Coating or Powder Coating